AI + Machine Learning, Announcements, Azure IoT, Digital Twins, Events, Internet of Things
Published • 4 min read
Azure IoT’s industrial transformation strategy on display at Hannover Messe 2024
Microsoft recently launched two accelerators for industrial transformation: Azure’s adaptive cloud approach and Azure IoT Operations. These accelerators will be on display at Hannover Messe 2024 from April 22 to April 26, 2024.
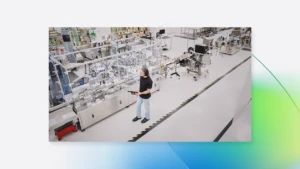